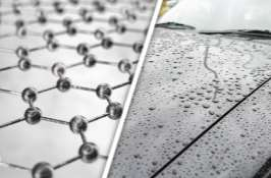
Graphene Coating
Graphene, a single layer of carbon atoms arranged in a two-dimensional honeycomb lattice, has emerged as a revolutionary material in the world of advanced coatings. With unparalleled strength, electrical conductivity, and thermal properties, graphene coatings offer a myriad of possibilities for enhancing the performance and durability of various surfaces. In our lab, we delve into the intricacies of plasma spray techniques to apply graphene coatings with precision and efficiency. From enhancing corrosion resistance to improving wear and tear properties, our research endeavours aim to unlock the full potential of graphene in diverse industrial applications. Explore the forefront of materials science with our graphene coating research, where innovation meets functionality.
Tailoring Wettability
In the dynamic realm of surface engineering, our lab takes a pioneering step forward with our research on tailoring wettability. Wettability, the ability of a liquid to spread across or adhere to a solid surface, plays a crucial role in numerous industrial applications, from manufacturing to medical devices. Our researchers are dedicated to unlocking the secrets of tailoring wettability through advanced plasma spray coating techniques. By precisely manipulating surface properties, we aim to achieve custom levels of hydrophobicity or hydrophilicity, catering to the specific needs of diverse industries. Imagine surfaces that repel water, preventing corrosion and enhancing durability, or substrates that promote adhesion, revolutionizing biomedical implants. Our work in tailoring wettability opens doors to a spectrum of possibilities.
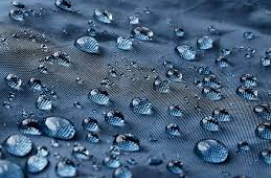
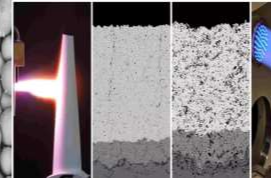
Thermal Barrier Coatings
Explore the cutting-edge world of Thermal Barrier Coatings (TBCs) with our laboratory's forefront research and applications. Our team focuses on developing and advancing TBC technologies to enhance the performance and durability of components exposed to high temperatures. TBCs, comprising a substrate material, bond coat, and ceramic topcoat, play a pivotal role in providing thermal insulation, oxidation and corrosion resistance, and ensuring thermal expansion compatibility. Our expertise extends to diverse applications, including gas turbine engines, automotive exhaust systems, and power generation components. By addressing challenges related to durability, deposition techniques, and cost optimization, we are at the forefront of pushing the boundaries of TBC innovation. Join us in exploring the crucial role TBCs play in extending the lifespan and efficiency of components in extreme temperature environments.
Nitride Coatings
Discover the transformative power of Nitride Coating as we delve into the realm of advanced surface enhancement. Applied through cutting-edge methods such as physical vapor deposition (PVD) or chemical vapor deposition (CVD), nitride coatings bring a new dimension to material performance. With exceptional hardness and wear resistance, components coated with nitrides excel in durability, making them ideal for industries where reliability is paramount. These coatings also provide a robust defence against corrosion, extending the lifespan of materials and reducing maintenance costs. Nitride coatings contribute to improved thermal stability, enabling materials to withstand high temperatures without compromising structural integrity. Our lab, at the forefront of materials science, employs precision engineering to ensure optimal coating thickness and uniformity. From aerospace to medical devices, nitride coatings find versatile applications, pushing technological frontiers and redefining standards in surface engineering. Explore the possibilities with our nitride coating solutions as we continue to innovate and elevate materials to unprecedented heights.
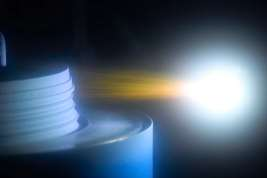
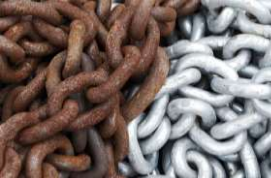
Corrosion Resistant Coatings
At our Plasma Spray Coating Lab, our Corrosion-Resistant Coatings stand as guardians, shielding surfaces from the corrosive forces of moisture and chemicals. With versatile applications spanning industries, these coatings not only extend the lifespan of materials but also reduce maintenance costs through precision application techniques. Our commitment to sustainability is reflected in environmentally friendly formulations, ensuring enduring performance against the persistent threat of corrosion. Join us in fortifying surfaces for a lasting impact.
Wear Resistant Coatings
Explore the intersection of innovation and material science in our Plasma Spray Coating Lab with our Wear-Resistant Coatings. Expertly engineered to counter friction and abrasion challenges, these coatings showcase a triumph in material science. Tailored for enduring performance, they prove indispensable in industries facing constant wear and tear on machinery. Versatile across sectors, these coatings extend component lifespan, embodying the forefront of material science research with cutting-edge materials and precision application. Join us on the cutting edge, where innovation and material science converge to redefine durability and fortify components against the test of time and usage.
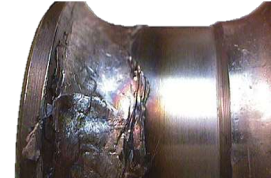
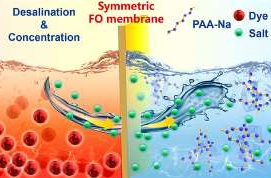
Ceramic Coating for Superior Water Treatment
Embark on a journey of innovation in water treatment at our Plasma Spray Coating Lab, where our specialized ceramic coatings redefine standards. Engineered for enhanced corrosion resistance, improved efficiency, and high-temperature stability, these coatings elevate the reliability and performance of water treatment components. With anti-fouling properties and exceptional chemical resistance, our ceramic coatings ensure sustained effectiveness, contributing to sustainability goals by extending component life. Join us at the forefront of innovation, where our ceramic coatings play a pivotal role in optimizing water treatment efficiency and durability.
Composite Coating for Supercapacitor Applications
Embark on a journey of enhanced energy storage capabilities with our specialized Composite Coating designed for supercapacitor applications. Crafted at our Plasma Spray Coating Lab, this innovative solution is tailored to elevate both efficiency and durability. By seamlessly integrating advanced materials, our composite coating ensures superior conductivity, structural stability, and resistance to wear, corrosion, and thermal stress. Beyond increasing energy storage capacity, this transformative coating guarantees consistent performance across various environmental conditions. Join us in reshaping the future of efficient and durable energy storage solutions with our pioneering Composite Coating technology.
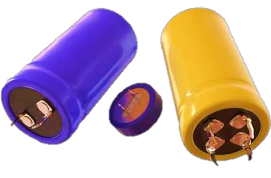
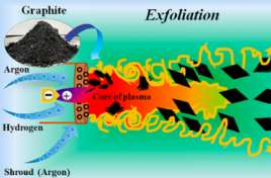
Exfoliation of 2D Materials
Anup Kumar Keshri, a materials scientist and engineer at the Indian Institute of Technology Patna, and his team made graphene using plasma spraying, a well-established technique for depositing metal or ceramic coatings. The method involves melting powdered coating materials in a jet of plasma—a high-temperature gas of ions—and spraying them on a surface.The engineers loaded graphite particles in a plasma spray gun. The thermal shock from the 3,000 K temperature and the turbulent eddies in the resulting plume rip apart the graphite into graphene flakes. The researchers collected the sprayed powder, put it in deionized water, and spun it in a centrifuge to remove unexfoliated clumps of graphite. Analysis with a variety of microscopy and spectroscopy methods showed that the graphene flakes were up to 3 µm in diameter, with 85% being a single atomic layer and the rest having a few layers. The material was free of defects and had a high carbon-to-oxygen ratio of 21, comparable to graphene made using CVD—both of which are signs of good quality. Films made with the graphene flakes were strong and had a lower electrical resistance than films prepared using graphene made with other exfoliation techniques.